Mechanical Vapor Recompression
Zero Liquid Discharge Solutions With MVR
A mechanical vapor recompression vacuum evaporator is designed for the efficient treatment of industrial waste effluent from production processes and water treatment plant reject fractions (brine) with a low energy cost.
Its high efficiency is due to the use of a rotary blower or steam compressor, which increases its latent heat by the mechanical action of volumetric compression with a small amount of electrical energy used in the motor powering the compressor.
This heat from the compressed steam is supplied by a heat exchanger to
heat the effluent to evaporate and consequently condense the vapor to
produce distilled water. When working under vacuum, produced by the
rotary blower itself or by an auxiliary vacuum pump, the boiling and
steam temperatures range from 60°C to 90°C.
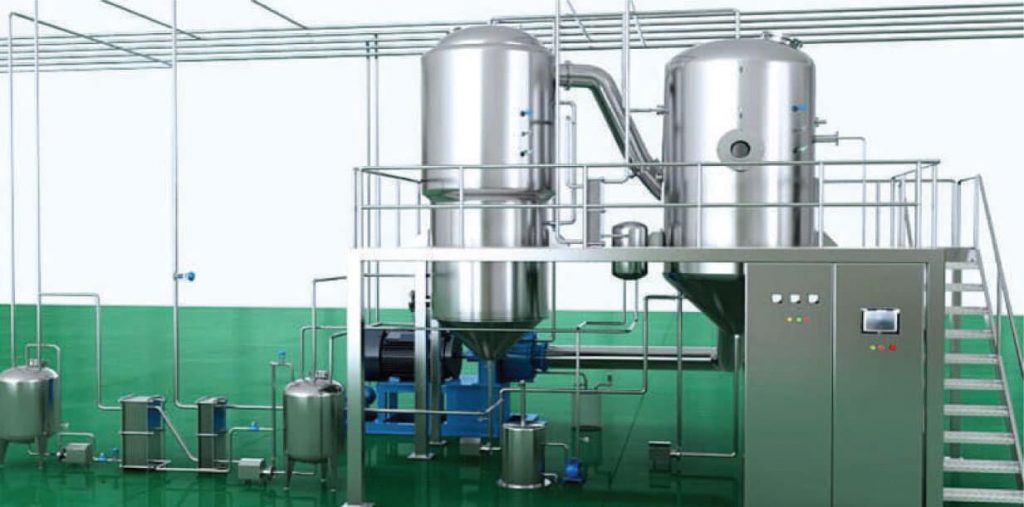
Vacuum evaporators separate high-quality water from a relatively concentrated contaminant phase by the application of thermal energy.
By using vacuum evaporators, waste effluent can be concentrated efficiently and easily as much as required, up to zero discharge if required. This technology can treat effluents that are not effective or viable to treat by the most conventional techniques due to their nature.
MVR evaporators operate on a “heat pump” principle. The evaporated water vapor is recompressed with a simple, low-speed centrifugal fan or compressor which increases the saturation of the vapor. After the fan, vapor can be used as heating steam in the same unit. The recompressed vapor condenses and releases its latent heat through the heat transfer surface for further evaporation of the liquor or effluent.
Working Principal
MVR is called Mechanical Vapor Recompression. It use the centrifugal compressor to re-compress the secondary vapor which is evaporated from the liquid material to rise its pressure, so as to reuse it as heating source to evaporate the liquid material again. The process is to convert a small amount of electric energy to more heat energy. Theoretically, compared with multi-effect evaporator, it can save more than 50%~80% energy consumption and 90% cooling water.
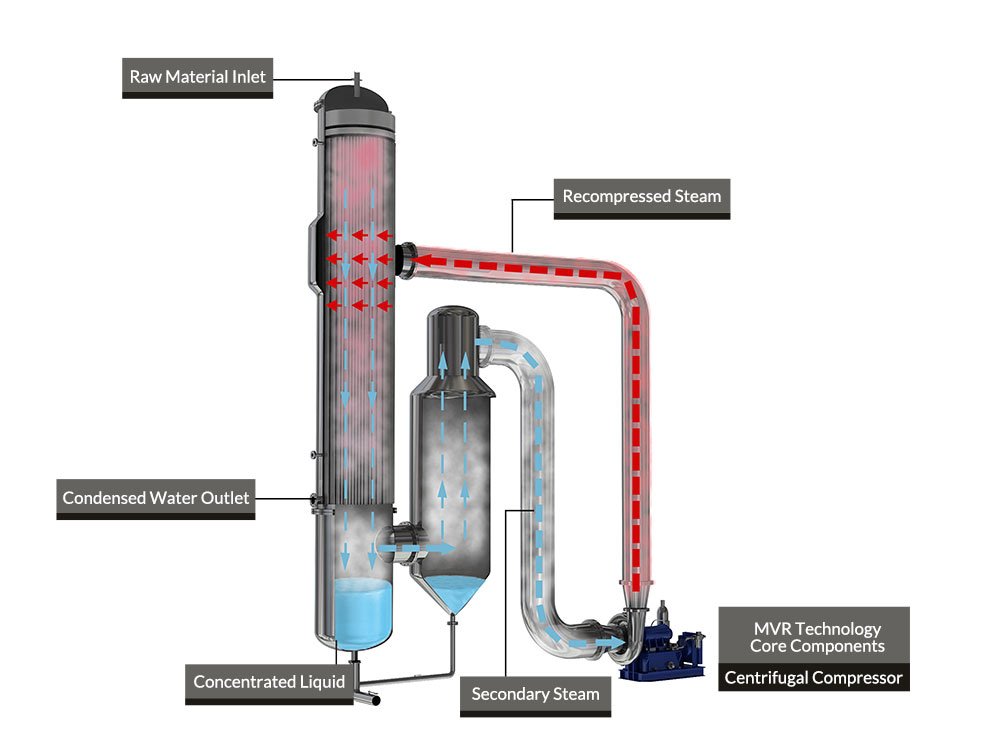
Comparison MVR VS MEE
NO | Item | MVR Evaporator | Three Effect Evaporator |
---|---|---|---|
1 | Operation Difficulty | High Automation, less Equipment, operation Easy | High Automation,more equipments, operation difficult, More Falut Point,one effect have problem,whole system need stop for maintenance,less Economic |
2 | Occupation Area | Small | Big |
3 | Investment | High | 30% Lower Than MVR |
4 | Energy Costs | Low,around 74% Compared with three effect | High |
5 | Water Consumption | Less(pump seal water cooling) | Big (three effect secondary steam cooling) |
6 | Application | Low boiling pint arise, 5-10℃ | Could evaporate high boiling point material |
7 | Affect on quality of product | stay time is short, minimum effect on quality of product | Stay time is longer, small effect on quality of products |